Base Oil Technology
Vertex Refining OH, LLC operates a non-hazardous, used oil refinery in Columbus, Ohio as well as four terminals scattered throughout the Midwest, which aggregate used motor oil (UMO) collected from 8-10 major metropolitan areas. Nestled in the heart of the Midwest, the refinery sits on almost five acres of land just a five-minute drive from Port Columbus International Airport in Columbus. Our services include used oil pickup and removal, oil filter management, used antifreeze disposal, No.4 fuel sales, asphalt flux sales diesel additive sales, and Group II base oil sales.
Vacuum Gas Oil Production
With our state-of-the-art vacuum distillation unit, the refining group has the capability and capacity to convert 1,500 barrels per day of used motor oil into vacuum gas oil. We use a two-step process to separate useful vacuum gas oil (VGO) from the waste products in spent passenger car used motor oil. In the first stage, the distillation unit removes water and the light oils, under a moderately high vacuum and temperature. These two streams are then separated in a decanting vessel and sent to storage. The remaining used motor oil is refined through a series of short-path wiped film evaporators at progressively higher temperatures and deeper vacuums to extract the vacuum gas oil from the thicker residual materials in the oil. In this step, the used motor oil is fed above the heated zone into the wiped film evaporator and is evenly distributed over the evaporator’s inner surface by a rotor with fixed blades. As the product spirals down the heated wall, a bow wave developed by the rotor blades generates highly turbulent liquid film, which results in optimum heat and mass transfer. The volatile components are vaporized and condensed on an inner water-jacketed tube bundle, and the nonvolatile components are discharged at the bottom of the wiped film evaporator. This, in turn, results in an asphalt oil residual byproduct and finished vacuum gas oil, which can be further processed or sold as a refinery grade intermediate (How Thin Film Evaporators Work).
Catalytic Hydrotreating (Base Oil Production)
The hydrotreating unit takes the vacuum gas oil feed from the vacuum distillation unit and hydrotreats it in a hydrogen rich environment under high temperatures and pressures to produce a clean 150N Group II base oil and diesel fuel additive. This process removes about 90% of contaminants such as nitrogen, sulfur, oxygen and metals from the vacuum gas oil while converting olefins and aromatics to saturated compounds. Our unit consists of three reactors in series. The first two reactors serve as guard beds removing most of the metals, silica and phosphorus from the vacuum gas oil. In the third reactor, the desulfurization and deoxygenation chemical reactions take place. After the oil has been hydrotreated in the reactors, the unused hydrogen and hydrogen sulfide byproduct are separated from the oil in a series of knockout drums. The unused hydrogen is recycled, and most of the hydrogen sulfide is burned in the unit’s process heater. The base oil is further refined by removing the lightest portion of oil through a vacuum stripper column. The oil is then cooled and sold as our final product.
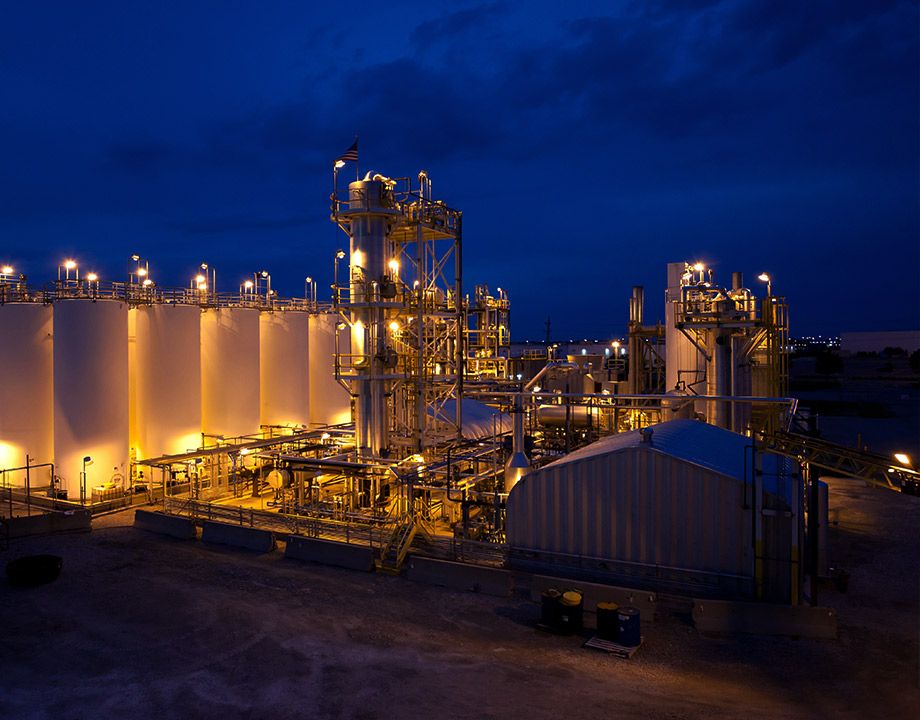